Optimize Mass Production Processes For Efficiency, Quality, And Scalability
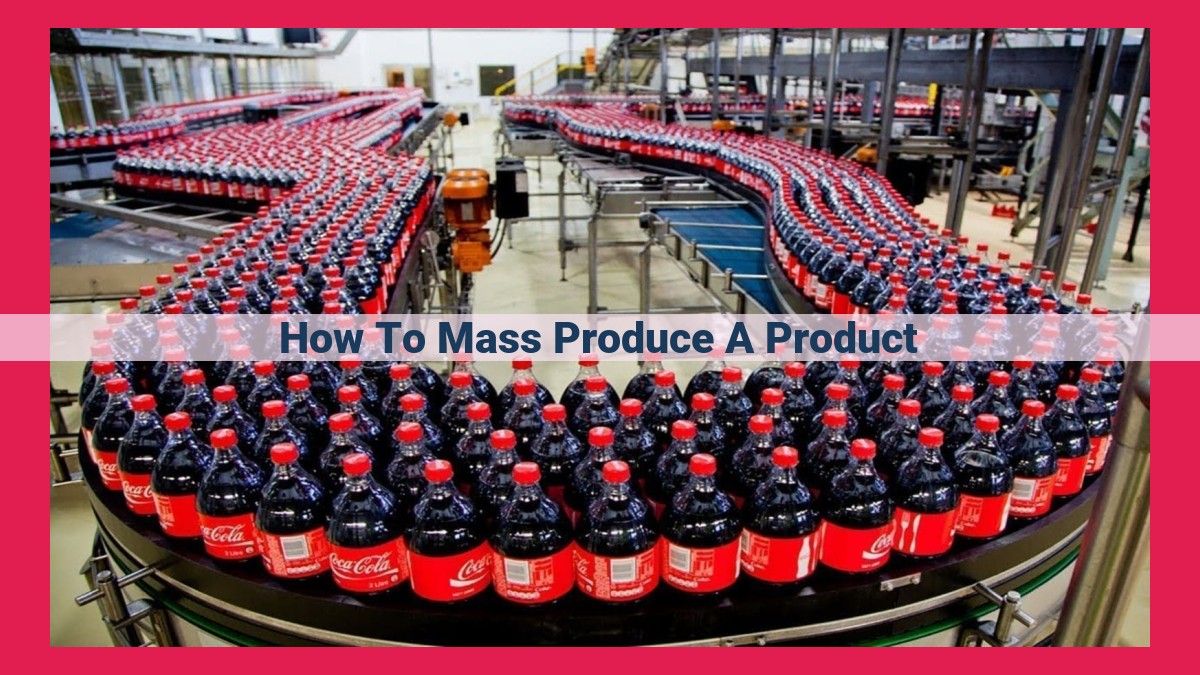
Mass production involves meticulous planning, efficient processes, and rigorous quality control. Through effective resource allocation, equipment selection, and capacity planning, businesses can optimize production. Inventory management, automated systems, and lean practices minimize waste and enhance efficiency. Quality standards, Six Sigma analysis, and statistical controls ensure product quality. By leveraging automation, Just-in-Time principles, and mass customization, businesses can scale production while meeting diverse customer needs.
Production Planning: The Art of Orchestrating Manufacturing Success
Amidst the bustling symphony of manufacturing, production planning emerges as the conductor, orchestrating a harmonious balance of resources, schedules, and meticulous quality control.
Resource Allocation: The Strategic Arrangement
Like a skilled chess master, effective resource allocation anticipates future demands and astutely distributes assets. It assigns the right people, materials, and equipment to the right tasks at the right time. By aligning resources with production goals, it ensures smooth operations and maximizes efficiency.
Production Scheduling: The Symphony of Time
Production scheduling choreographs the sequence of manufacturing tasks. It determines the flow of materials through the production line, setting deadlines for each stage and optimizing production time. By synchronizing operations, scheduling minimizes bottlenecks and keeps the production process humming like a well-tuned orchestra.
Quality Control: The Guardian of Excellence
Quality control acts as the vigilant sentinel of manufacturing excellence. It establishes strict standards, monitors production processes, and promptly identifies and rectifies defects. By safeguarding product quality, it protects the reputation of the company and ensures customer satisfaction, becoming the cornerstone of a successful manufacturing operation.
Process Design:
- Outline the step-by-step manufacturing process, including equipment and materials requirements.
Process Design: The Blueprint for Efficient Manufacturing
Every manufacturing endeavor begins with a meticulously crafted process design, the roadmap that guides the journey from raw materials to finished products. This vital stage lays the foundation for efficiency, quality, and cost-effectiveness throughout the production lifecycle.
Step-by-Step Manufacturing Process
-
Raw Material Procurement: Sourcing the right materials from reliable suppliers is crucial to ensure the quality and consistency of finished products.
-
Preprocessing: Depending on the nature of the raw materials, preprocessing steps such as cleaning, sorting, and shaping may be necessary to prepare them for further processing.
-
Fabrication: This stage involves transforming raw materials into components or parts using various techniques such as cutting, forming, welding, or casting.
-
Assembly: The fabricated parts are then assembled into the final product. This step requires meticulous attention to detail and precision to ensure proper fit and function.
-
Finishing: The final product undergoes finishing processes such as painting, coating, or polishing to enhance its appearance and durability.
-
Packaging: The finished product is carefully packaged to protect it during transportation and storage.
Equipment and Materials Requirements
The selection of appropriate equipment and materials is paramount to the efficiency and quality of the manufacturing process. Factors to consider include:
-
Equipment Capabilities: The equipment must be capable of performing the required tasks with precision and efficiency.
-
Materials Properties: The materials used must meet the specifications of the final product in terms of strength, durability, and other characteristics.
-
Safety Considerations: The equipment and materials must meet all safety regulations to ensure the well-being of workers.
By carefully designing the manufacturing process and selecting the right equipment and materials, businesses can optimize efficiency, minimize waste, and deliver high-quality products to meet customer demands.
Capacity Planning: Meeting Production Needs
In the realm of manufacturing, capacity planning stands as a crucial pillar, ensuring a seamless flow of production and optimal resource utilization. It involves a meticulous assessment of demand forecasting to anticipate future production requirements. Once demand is understood, the next step is to conduct a resource assessment. This entails taking stock of existing production capabilities, machinery, manpower, and raw materials.
Based on the demand forecast and resource assessment, capacity planning establishes a blueprint for meeting production needs. This involves determining the optimal production schedule, adjusting operations to match demand fluctuations, and identifying potential bottlenecks or overcapacity situations.
Effective capacity planning requires flexibility and the ability to adapt to changing market conditions. By proactively aligning production capabilities with demand, manufacturers can avoid costly overproduction or missed opportunities due to insufficient capacity. Moreover, it lays the foundation for cost optimization, efficient resource allocation, and timely delivery of products to customers.
Inventory Management: The Art of Keeping the Flow
In the fast-paced world of manufacturing, inventory management plays a pivotal role in maintaining smooth operations and maximizing efficiency. It’s like a delicate balancing act, where you need to keep the shelves stocked without overordering or running out of essential parts.
Stock Level Optimization
The key to inventory management is finding the optimal stock level, where you have enough supplies to meet demand without tying up too much capital in unused stock. It’s a delicate equilibrium that requires careful planning and forecasting.
Inventory Control Systems
Once you’ve determined your optimal stock levels, it’s time to implement an inventory control system to track and manage your inventory. These systems can be as simple as a spreadsheet or as complex as an enterprise software suite. The right system for you will depend on the size and complexity of your operation.
Replenishment Strategies
Finally, you need to determine your replenishment strategy, which is how you decide when and how much inventory to reorder. There are several popular strategies, including:
- Periodic Review: Ordering inventory at regular intervals, regardless of stock levels.
- Continuous Review: Monitoring stock levels and ordering inventory when they reach a predetermined point.
- Kanban: Using visual cues to trigger replenishment when inventory reaches a low level.
The Bottom Line
Effective inventory management is crucial for manufacturing success. It helps you avoid costly stockouts, optimize cash flow, and improve overall operational efficiency. By carefully planning your stock levels, implementing the right control systems, and choosing the best replenishment strategy, you can keep your production running smoothly and your customers satisfied.
Quality Control: Maintaining Excellence in Production
When it comes to manufacturing, quality is paramount. Customers expect products that meet their expectations, and businesses rely on consistent production of high-quality goods to maintain customer satisfaction and gain a competitive edge.
Strict Quality Standards
At the heart of effective quality control lies a well-defined set of quality standards. These standards outline the specifications and tolerances that each product must meet or exceed. By establishing clear guidelines, manufacturers can ensure that their products consistently meet customer expectations.
Regular Inspections
To verify that products meet quality standards, regular inspections are a crucial part of the quality control process. These inspections can be conducted at various stages of production, from raw material verification to finished product testing. By identifying and correcting defects early on, manufacturers can prevent faulty products from reaching customers.
Corrective Actions
When quality issues arise, it is essential to take swift and effective corrective actions. This involves identifying the root cause of the problem and implementing measures to prevent it from recurring. Continuous improvement methodologies, such as Six Sigma, can be used to enhance the quality control process and identify areas for improvement.
By adhering to strict quality standards, conducting regular inspections, and taking corrective actions when necessary, manufacturers can ensure the production of high-quality products that meet customer expectations. This not only enhances customer satisfaction but also strengthens the brand reputation and drives business success.
The Transformative Power of Automation in Production
Introduction:
In today’s rapidly evolving manufacturing landscape, automation has emerged as a game-changer, revolutionizing the way businesses operate. From robotics to machine learning and system integration, automation is unlocking unprecedented levels of efficiency, accuracy, and productivity.
Benefits of Robotics:
Robots are transforming production lines by performing repetitive tasks with precision and speed that far exceed human capabilities. They eliminate the risk of human error, reduce labor costs, and increase overall production output. Robotics also enables manufacturers to handle hazardous or delicate tasks that would pose safety risks for human workers.
The Promise of Machine Learning:
Machine learning algorithms are transforming data into actionable insights, helping manufacturers predict demand, optimize resource allocation, and identify potential bottlenecks. By analyzing historical data and real-time conditions, machine learning systems can make intelligent decisions that improve production efficiency, reduce downtime, and minimize waste.
System Integration:
Connecting disparate systems and equipment through system integration creates a holistic production ecosystem. This seamless flow of information enables manufacturers to monitor operations in real-time, identify and address inefficiencies, and make adjustments based on data-driven insights. System integration optimizes resource utilization, reduces production time, and enhances overall productivity.
Conclusion:
Automation is redefining production processes, empowering manufacturers with new levels of efficiency, accuracy, and flexibility. By embracing the transformative power of robots, machine learning, and system integration, businesses can stay ahead of the competition, increase profitability, and drive innovation in the ever-evolving manufacturing industry.
Lean Manufacturing: A Journey to Operational Excellence
In the relentless pursuit of efficiency, lean manufacturing has emerged as a beacon of innovation, transforming production processes to achieve unparalleled levels of productivity and quality. Its principles are rooted in the unwavering belief that waste is the enemy of progress, and continuous improvement drives lasting success.
At the heart of lean manufacturing lies the concept of waste elimination. The process begins with meticulously identifying and eliminating inefficiencies at every stage of production. By closely scrutinizing each step, businesses can streamline their operations, reducing bottlenecks and maximizing value.
Complementing the focus on waste reduction, lean manufacturing emphasizes the power of continuous improvement. It fosters a culture where every member of the team is encouraged to identify areas for optimization and make suggestions for improvement. By fostering a spirit of accountability and empowerment, lean organizations create an environment where innovation thrives and incremental changes accumulate into transformative outcomes.
The ultimate goal of lean manufacturing is to achieve operational excellence. This encompasses not only streamlined processes but also the unwavering pursuit of quality, flexibility, and customer satisfaction. Lean organizations cultivate a lean mindset that permeates every aspect of their operations, from raw material procurement to product delivery.
By embracing the principles of waste elimination, continuous improvement, and operational excellence, lean manufacturing empowers businesses to achieve remarkable results. It reduces costs, improves quality, enhances productivity, and fosters a culture of innovation and accountability. In a rapidly evolving industrial landscape, lean manufacturing stands as a proven path to sustained success and enduring competitiveness.
Just-in-Time Production:
- Describe Kanban systems, reduced inventory levels, and improved production flow.
Just-in-Time Production: A Symphony of Efficiency and Customer Delight
In the dynamic world of manufacturing, Just-in-Time (JIT) production emerges as a maestro, orchestrating a harmonious flow of resources to meet customer demands with unmatched precision. Like a conductor leading an orchestra, JIT eliminates excess inventory and waste, ensuring a seamless interplay between production and consumption.
Kanban: The Guiding Force
At the heart of JIT lies the Kanban system, a visual and intuitive communication tool that transmits signals throughout the production process. Each Kanban card represents a specific quantity of raw materials or finished goods, acting as a beacon guiding the flow of materials through the production line. By limiting the number of cards in circulation, JIT ensures a delicate balance between supply and demand, preventing overproduction and minimizing inventory bloat.
Reduced Inventory Levels: The Key to Agility
JIT emphasizes the concept of “pull production,” where production is triggered only when demand arises. This approach drastically reduces inventory levels, freeing up valuable space and capital. By eliminating excess inventory, companies gain the agility to adapt quickly to market fluctuations and customer preferences. They can introduce new products or modify existing ones without the burden of surplus stock.
Improved Production Flow: A Symphony in Motion
The reduced inventory levels fostered by JIT pave the way for a smooth and uninterrupted production flow. By eliminating bottlenecks and unnecessary delays, manufacturers can achieve a consistent pace and rhythm in their operations. This streamlined flow ensures timely delivery of products, meeting customer expectations and enhancing overall efficiency.
The Benefits of JIT: A Harmony of Advantages
The symphony of JIT production resonates with a multitude of benefits, including:
- Reduced production costs: Lower inventory levels and waste reduction lead to substantial cost savings.
- Improved product quality: The focus on continuous improvement and quality control leads to higher-quality products.
- Faster delivery times: By eliminating bottlenecks, JIT enables faster order fulfillment, enhancing customer satisfaction.
- Increased flexibility: The ability to adapt to changing market demands provides a competitive edge and fosters innovation.
Just-in-Time production is a masterpiece of manufacturing excellence, a carefully choreographed dance that synchronizes production with customer needs. By embracing the principles of Kanban, reducing inventory levels, and optimizing production flow, manufacturers can unlock a symphony of efficiency, quality, and customer delight.
Six Sigma: A Proven Methodology for Process Improvement
Embrace the Power of Statistical Analysis
In the realm of production management, Six Sigma stands tall as a rigorous methodology that harnesses the power of statistical analysis to achieve unprecedented levels of quality and efficiency. By employing a data-driven approach, Six Sigma empowers organizations to identify and eliminate defects, stabilize processes, and drive down costs.
Defect Detection: Precision and Accuracy
At the heart of Six Sigma lies its ability to meticulously analyze data to pinpoint defects and quality deviations. Statistical tools such as control charts and process capability studies provide a clear understanding of process performance, allowing for early detection of potential problems. By focusing on reducing defects, Six Sigma minimizes disruptions, improves product quality, and enhances customer satisfaction.
Process Stability: A Foundation for Success
Beyond defect detection, Six Sigma emphasizes process stability as a cornerstone of operational excellence. Through meticulous analysis, practitioners strive to identify and eliminate sources of variation that can destabilize processes. By controlling critical parameters and establishing robust manufacturing methods, Six Sigma helps organizations achieve consistent, predictable results. A stable process is less prone to defects, leading to increased efficiency, reduced waste, and improved profitability.
Cost Reduction: Unlocking Hidden Savings
The benefits of Six Sigma extend far beyond improved quality. By eliminating defects and optimizing processes, organizations can significantly reduce costs. Wasteful practices, unnecessary rework, and downtime are minimized, resulting in leaner operations and enhanced profitability. Six Sigma provides a clear roadmap for identifying and addressing cost drivers, unlocking hidden savings that can fuel business growth.
Six Sigma is not merely a tool but a mindset that fosters continuous improvement, innovation, and operational excellence. By embracing statistical analysis, defect detection, process stabilization, and cost reduction, organizations can transform their production processes and drive tangible results. In the competitive landscape of today’s business environment, Six Sigma remains an indispensable ally for those seeking to achieve the highest levels of quality, efficiency, and customer satisfaction.
Mass Customization: Empowering Personalization in Production
In today’s customer-centric era, the demand for personalized products has surged. Mass customization has emerged as a revolutionary manufacturing approach that empowers businesses to cater to individual preferences while maintaining efficiency.
Concept of Personalization:
Mass customization allows customers to design and order products tailored to their specific requirements. This paradigm shift from mass-produced goods to personalized offerings empowers consumers to express their individuality and create products that truly reflect their tastes and needs.
Advanced Manufacturing Techniques:
To support mass customization, advanced manufacturing technologies such as 3D printing, laser cutting, and computer-aided design (CAD) play a pivotal role. These technologies enable the rapid prototyping and production of customized products with intricate designs and precise dimensions.
Market Demand Fulfillment:
Mass customization addresses the evolving market demand for varied products in smaller quantities. By eliminating the need for large production runs, businesses can respond swiftly to customer requests and fulfill niche market needs. This flexibility ensures that producers remain agile and competitive in a dynamic market landscape.
Benefits for Businesses:
Mass customization offers numerous benefits to businesses:
- Increased customer satisfaction through personalized experiences
- Creation of a competitive advantage by offering unique products
- Reduced inventory levels and production costs
- Improved operational efficiency and responsiveness to market demands
Mass customization is a game-changer in the manufacturing industry, empowering businesses to meet the evolving demands of today’s consumers. By embracing advanced manufacturing techniques, businesses can provide personalized products, fulfill market demand, and drive innovation. This approach promises to reshape the way we manufacture and consume goods, creating a win-win situation for both businesses and customers alike.